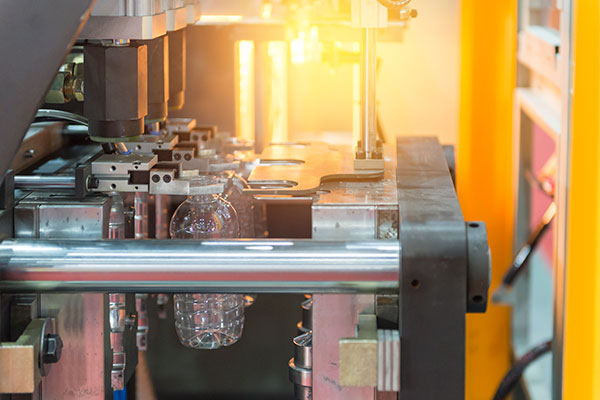
What is the Blow Molding Process?
When you need to create plastic products that have a hollow center, such as bottles, pharmaceutical packaging, cosmetics containers, and storage containers, blow molding is the best way to go. With blow molding, you can turn the raw, base plastic into the forms that you need. Here are the basics of the process to help you understand how it works.
Preparing The Plastic
The very first step in the process is to prepare the plastic for molding. If the plastic is being molded in its natural state, there’s little preparation to do. However, you can also incorporate colorings, chemical additives, and other materials.
In either case, whether you’re using the plastic as-is or adding other components, it’s sent through a material handling system that either distributes the plastic directly to the molds or incorporates the additives and creates a precise blend of the raw plastic, the coloring, and any other additives that you’re using.
During this preparation process, you can even incorporate the reclaimed plastic material into your molding mixture. This is great for minimizing your environmental footprint and recycling old plastic material.
Once the mixture is combined in the handling stage, the final molding plastic is moved into a hopper that is mounted to the molding machine. This allows for transitioning the plastic into the next stage of the process.
Extruding The Plastic
The hopper that’s mounted to the molding machine has an extruder attached. That extruder is what sends the plastic into the first stage of actually molding the bottle or container. The plastic mixture created in the handling stage is moved along the barrel of the extruder by a screw inside the extruder unit. The screw turns constantly, forcing that plastic mixture through the system.
During that movement, friction is created. Heat caused by that friction, along with heaters that warm the barrel, will transition the plastic pellets into a melted, molten form. The heaters create a consistent temperature all the way through the barrel, so by the time the plastic reaches the end of the extruder, it is in a uniform liquid state. At the very end of the extruder, that molten plastic moves through the extruder head. This forces the plastic through a die that creates the initial form.
Creating The Initial Parison
A parison, which is a hollow plastic tube, is the beginning of the physical mold. You can alter the size and shape of the parison by modifying the extruder head and the die tooling that’s used to create it. If you’re creating large bottles or pieces, you may want to make them one at a time using large extrusion heads. On the other hand, if you’re making smaller pieces, you may be able to use extrusion heads that can create several parisons per extrusion cycle.
Making The Final Mold
Once the parison is created, it gets secured inside the mold. The molds are usually created from metal because that allows for rapid cooling once the plastic is fully molded. A pin is inserted into the top of the parison. Compressed air is forced through to push the plastic outward into the shape of the mold. Once it is properly molded, the plastic is cooled so that it hardens. After the hardening phase, the mold is opened and the completed product is removed.
Dealing With Excess Plastic
In every molding process, there’s excess plastic that’s left in the mold. It can be removed mechanically or manually, but it needs to be removed from the mold to be reused. Once the plastic is removed, it can be ground back up into smaller pieces and then mixed into the beginning stage of the production process. This recycles the excess plastic, reducing or nearly eliminating your production waste.
Valencia Plastics offers a full range of plastics production services including blow molding, injection molding, and mold making. We proudly serve the medical, aerospace, defense, automotive, electronics, and consumer industries. We can provide guidance and engineering services in-house for inventors and new product development so don’t hesitate to contact us for all your plastic production needs.
Previous Article
How to Decide if You Really Need To Have A Custom Molded Plastic Bottle
0 Comments
Leave a reply
You must be logged in to post a comment.