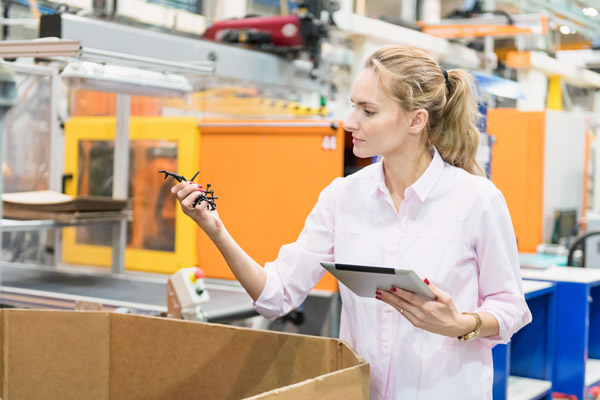
Four Signs It’s Time to Replace Your Tools
Injection molding tools should be cleaned and repaired regularly to keep them in their best condition. Without tool maintenance, the quality of plastic components can be affected as well as the project’s budget. Even though molds are made to withstand the tear and wear that occurs, they still undergo a lot of stress, and over time, tool repair and replacement will be needed to ensure your finished product’s quality is not affected.
How do you know the right time to replace your tool? The best way to find out is by examining the following factors that affect the tool’s functioning.
1. Bad Parts
Tools have different parts that must fit harmoniously for the mold to work. These parts have narrow specifications. When the pieces no longer fit, it means the tool cavities are worn. If the elements affect the finished product, then the tool needs to be repaired or replaced.
2. Flash
Flash is the plastic material that seeps into the gaps between the molding parts. Small amounts of residue can accumulate inside the mold cavities depending on the number of completed cycles the mold makes. Over time, the accumulation of this residue can affect the interior cavity shape and eventually, the finished part’s shape as well. Flash removal is a necessary part of the blow molding process.
3. Material Composition
Soft tools have less cycles in their life span than hard tools. Also, different types of resin wear out the tools at different rates. To enhance the performance of the molded part, most materials contain additives. Certain materials require fiberglass and lubrication embedded in the finished product for specific reasons. Glass and lubrication can cause abrasive conditions that tend to be aggressive to components in the mold and also the machine barrel.
Additionally, the chemical makeup of the different materials used can also have undesired interactions with the mold, affecting the integrity of the final product. Some materials are corrosive, reacting with the heat and moisture, and over time, deteriorating the integrity of the mold.
4. High Temperature and Pressure
High temperatures can affect seals found in the valve pin actuator in a valve-gate hot runner system. With such systems, it is recommended that you leave the mold cooling on after shutting down the hot runner. Exposing the seals to temperatures higher than the specifications will degrade them.
Also, if the mold design does not allow uniform cooling, the temperature fluctuations can cause it to expand and contract. The expansion and contraction cause weakening or even cracking.
The mold’s moving parts tend to undergo friction and mechanical breakdown. The friction on top of the heat might wear out parts of the mold resulting in compromised contact points or the creation of undesired cavity shapes. If a mold does not smoothly open and close, impact stress occurs when the two halves meet. After several molding cycles, the ejector pins might also not work as intended.
Regularly monitoring the condition of your mold allows you to identify potential issues such as repair or replacement. Maintenance costs will always be less than replacing a tool but in some cases, replacing the tool is the best solution. If you’re looking for professional help with your molding tools, please contact Valencia Plastics and let our experts help you through the process.
Previous Article
Blow Molding vs. Injection Molding
0 Comments
Leave a reply
You must be logged in to post a comment.